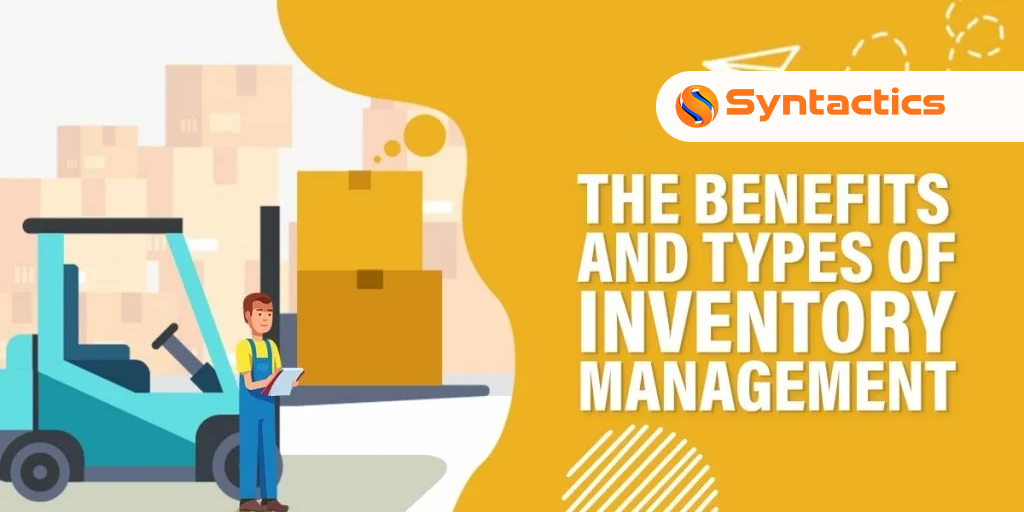
Inventory Analysis Methods: Types and Benefits
A thorough inventory analysis allows businesses to determine the right amount of stock to keep while considering their respective customer demands. Thus, Inventory Analysis Methods can help them examine their stock!
The inventory analysis process allows businesses to avoid spending too much on storage. But, you must use a balance sheet to analyze the carrying costs of goods sold, on hand, and for order. As such, it is essential to practice systematic and real-time analysis of the amount of inventory you have.
Through comprehensive analysis methods, you have better control over stock when running your business. We’ll explain some common analysis methods you can use for your business and their benefits.
Source: Zippia.
What are the Benefits of Inventory Analysis?
When you analyze inventory, you allow for a better Return On Investment. ROI determines whether a company meets its money rules and is still worth continuing its operations. Also, through inventory analysis, you help significantly reduce lost sales.
You can do this because inventory analysis allows you to identify the Inventory Stock Levels to keep on hand. Consequently, these are the goods or products you deem more likely to sell. Moreover, you also help increase customer loyalty because you can provide the products they need since you keep finished goods.
Here are other ways analyzing inventory helps your business:
- Establishing a proper warehouse layout;
- Reducing lead time in acquiring raw materials and sellable items;
- Implementing proper authorization;
- Accurate item classification for better cost management;
- Adequate management of dormant inventory items;
- Improving utilization of capital;
- Improving cash flow and profit margins, and
- Future identification of possible opportunities or losses.
Inventory analysis methods are crucial to your business. They contribute greatly to your Inventory Manager’s decision on what steps to take to protect valuable assets. Also, inventory analysis, management, and product classifications can help improve your policies for better inventory control.
Furthermore, you can use an online inventory management system to streamline workflows.
What Common Inventory Analysis Methods Can I Use?
ABC Analysis
First, the ABC analysis method categorizes items into A, B, or C groups based on sales revenue, profit margins, and demand frequency. Here’s a quick breakdown of the groups:
- Category A — High-Priority, High-Value. High-priority, in-demand products fall under this category. Thus, they account for 10% of the total inventory on hand but contribute 70% of the total consumption value.
- Category B — Medium-Priority, Moderate-Value. These stocks account for 20% of total inventory, which accounts for about 20% of the total consumption value.
- Category C — Low-Priority, Low-Value. Lastly, these low-demand items account for 70% of total inventory, which accounts for only 10% of the total consumption value.
Source: QuickBooks.
It’s important to periodically review and update the analysis to reflect changes in the market and business priorities.
How to Use the ABC Analysis:
The ABC Inventory Analysis Method categorizes items based on their annual consumption value. Sometimes, inventory managers use the Pareto Principle for classification.
As such, an ABC analysis method classifies the essential items in a particular group, usually constituting a small portion of the total items. Then, the majority of the items – as a whole – will seem to be of minor significance. As a result, this analysis method helps organizations allocate resources efficiently by prioritizing critical items over less important ones.
You can further supplement this method with the XYZ analysis. It helps forecast the difficulty of selling a particular item. Therefore, X are those that are easier to sell, whereas Z classifies items that are most difficult to sell.
How to Do an ABC Analysis of Inventory:
The ABC analysis can result in better inventory management, cost reduction, and improved customer service. Here’s what you need to do to conduct a proper ABC analysis of your inventory:
1. First, gather data about each item, such as an item’s revenue, profit margin, etc.
2. Next, sort and rank the items based on their annual usage value.
3. Divide the sorted list of items into the A, B, and C categories.
4. Focus on strict inventory control for Category A items, moderate attention for Category B, and less management effort for Category C.
5. Ensure that you regularly review your stock to account for changes in market conditions.
6. Additionally, utilize inventory management software to automate reports so you can update your analysis.
Source: Grand View Research.
FSN or Fast-, Slow-, and Non-Moving Inventory Analysis
Then, we have another inventory analysis method you can use, the FSN analysis. Here’s a breakdown of the FSN:
- Fast Moving — items that are frequently issued/used. They have a high turnover rate.
- Slow Moving — items issued or used less for a certain period. These types of items have a relatively lower demand than fast-moving stocks. Also, they tend to remain in inventory for longer, requiring careful management to avoid overstocking or obsolescence.
- Non-Moving — items not issued/used for more than a particular duration. Of course, they have very low or no demand and may need to be liquidated, discounted, or disposed of.
What is FSN Analysis?
FSN analysis in inventory management classifies inventory-based quantity, consumption rate, and frequency of issues and uses. FSN analysis helps optimize inventory levels and improve overall management strategies. Here are its other benefits:
- Optimizing inventory levels;
- Managing capital;
- Reducing holding costs;
- Minimizing obsolescence, and
- Improving customer service.
How to Do an FSN Analysis:
Follow these steps to conduct a successful FSN analysis:
1. Gather historical data on the past year’s sales, consumption, and inventory levels.
2. Determine thresholds for each category to classify items.
3. Categorize items into Fast, Slow-, or Non-moving based on your thresholds.
4. Use spreadsheets or inventory management software to automate categorization. List each item, its sales or consumption data, and a formula to determine the threshold category.
5. Regularly review and refine analysis as market conditions change and take action to maintain optimal inventory mix.
Source: Meteor Space.
Of course, your business must tailor its analysis to current unique circumstances. Also, you should regularly revisit your categorization criteria to stay responsive to changing market conditions.
VED or Vital, Essential, and Desirable Analysis
Next, you can use the VED analysis method, where you organize the items into the following three categories:
- Vital — inventory that you need to keep in stock consistently. After all, vital stock is indispensable to the organization’s operations. For instance, not having these items in a healthcare setting will result in life-threatening situations.
- Essential — keeping a minimum supply of this inventory is enough, as they’re often necessary for emergencies. Stockouts for this item are unacceptable since they have more importance than desirable items. Still, they’re not as critical as the ones in the vital category.
- Desirable — though these items are convenient, they’re optional or non-critical. Operations can run with or without them. As a result, the unavailability of these items won’t pose an immediate threat to life.
What is VED Analysis?
VED Analysis is used primarily for inventory control in healthcare and medical supply chain management. It’s an Inventory Analysis Method whose classification depends on the user’s experience and perception. It classifies inventory according to the relative importance of certain items to other items, like spare parts.
VED Analysis helps organizations focus on vital items while minimizing effort and cost. This categorization is especially crucial in healthcare, where patient care and outcomes depend on available medications, medical equipment, and supplies.
VED Analysis helps organizations prioritize the procurement and management of materials. It’s vital to ensure the uninterrupted functioning of their systems or services. But, it’s best to create a comprehensive strategy when it complements other inventory management techniques, like ABC analysis.
How to Do a VED Analysis:
Follow these steps to conduct a VED analysis:
1. List all items to be identified and analyzed.
2. Collect data on item usage, impact on operations, and consequences of unavailability.
3. Define criteria for categorizing items into VED categories.
4. Next, assign the items to their proper classification.
5. Prioritize management and procurement efforts based on your categorization.
6. Regularly review and update categorization based on changing requirements or situations.
7. Lastly, you must incorporate findings into materials management and inventory control processes.
Hire Our Custom Software Developers
to Create an App for Your Company!
HML or High, Medium, and Low Analysis
Then, we have the HML analysis method. This method for inventory writes or lists down products or items under the following classifications:
- High Cost — items with high unit value critical to an organization’s operations. For instance, the unavailability of these items can result in significant disruptions. Thus, businesses should have a constant supply of these items.
- Medium Cost — items with medium unit value. Unavailability will cause disruptions but aren’t immediately life-threatening.
- Low Cost — items with low unit value. They’re non-critical, so a lack of supply is inconvenient at most.
What is HML Analysis?
The HML analysis method is a valuable approach for categorizing inventory according to a product’s unit price. It is often used in materials management and inventory control for healthcare and medical supplies.
As a result, it categorizes items or materials into High, Medium, and Low priority based on their impact on a business’ operations. This approach minimizes the effort and cost associated with low-priority items.
Source: Myos.
How to Do HML Analysis:
This Inventory Analysis Method is a valuable approach for materials management, especially in healthcare settings. Here’s how to conduct an HML analysis:
1. Identify all the items or materials you want to analyze.
2. Gather data on each item, including its usage, impact on operations, and the consequences of unavailability.
3. Define the criteria for categorizing items into the HML categories.
4. Assign items to the appropriate categories.
5. Create a document to record item categories.
6. Prioritize your management and procurement efforts accordingly.
7. Regularly review and update the categorization as needed.
8. Incorporate the findings into your inventory management processes.
SDE or Scarce, Difficult, Easily Available Analysis
Lastly, you can use the SDE analysis method. This is how you classify items using this type of Inventory Analysis Method:
- Scarce — usually imported items that require longer lead time and are often hard to find. Thus, management requires strategic planning and higher stock levels.
- Difficult — items that are more available than scarce ones. They require more than a fortnight but less than six months lead time to be available.
- Easily Available — readily available items. They’re abundant in the market, requiring appropriate inventory control measures.
Hire Our Custom Software Developers
to Create an App for Your Company!
What is SDE Analysis?
SDE analysis classifies materials based on the availability of an item and procurement difficulty. This prioritizes items and allocates resources effectively, depending on whether a material is freely available or scarce. It also considers the number of days of its lead time.
How to Do SDE Analysis:
SDE analysis helps optimize procurement and inventory management strategies. Here’s a guide to conducting an SDE analysis:
1. Identify all the items to analyze.
2. Collect data on each item, such as availability and procurement characteristics.
3. Define the criteria for categorizing items into the SDE categories.
4. Review items and assign them to one of the categories.
5. Create a document or spreadsheet to record each item’s categorization.
6. Prioritize your management and procurement efforts.
7. Regularly review and update the categorization as needed.
8. Incorporate the findings into your inventory management processes.
Test Out These Inventory Analysis Methods
There are plenty of ways to make your inventory management work more efficient. These Inventory Analysis Methods can significantly assist your business.
Moreover, consider working with an Online Inventory System to further streamline your materials management workflows.
So, determine which of these analysis methods is perfect for you and your business. Not only will you efficiently manage your inventory, but you also increase positive ROI!
GENERAL FAQS
What is Business Inventory Analysis?
An Inventory Analysis is a process that comprehends the mix of business processes while being aware of the demand for specific products.
What are the Main Benefits of Inventory Analysis?
Inventory analysis helps business managers decide how to protect valuable assets. It also improves inventory control policies and contributes to better Return On Investment (ROI).
What are the Other Benefits of Inventory Analysis?
The benefits of doing a business inventory analysis include the following:
- Reducing lead time in acquiring sellable items;
- Proper item classification to improve cost management;
- Management of dormant inventory items, etc.
What are the Common Inventory Analysis Methods?
There are five common methods:
- ABC;
- FSN;
- VED;
- HML, and
- SDE.
Comment 0